How to Recognize What is Porosity in Welding and Improve Your Method
How to Recognize What is Porosity in Welding and Improve Your Method
Blog Article
The Scientific Research Behind Porosity: A Comprehensive Guide for Welders and Fabricators
Understanding the complex mechanisms behind porosity in welding is crucial for welders and fabricators aiming for impeccable workmanship. As metalworkers explore the midsts of this phenomenon, they reveal a globe controlled by numerous aspects that affect the development of these minuscule voids within welds. From the composition of the base products to the ins and outs of the welding process itself, a wide variety of variables conspire to either intensify or reduce the existence of porosity. In this thorough guide, we will certainly unravel the science behind porosity, exploring its results on weld top quality and unveiling progressed methods for its control. Join us on this journey with the microcosm of welding flaws, where precision fulfills understanding in the quest of remarkable welds.
Recognizing Porosity in Welding
FIRST SENTENCE:
Examination of porosity in welding exposes important insights right into the honesty and top quality of the weld joint. Porosity, characterized by the visibility of dental caries or spaces within the weld metal, is a typical problem in welding processes. These spaces, if not appropriately dealt with, can endanger the structural honesty and mechanical residential properties of the weld, leading to prospective failures in the ended up item.
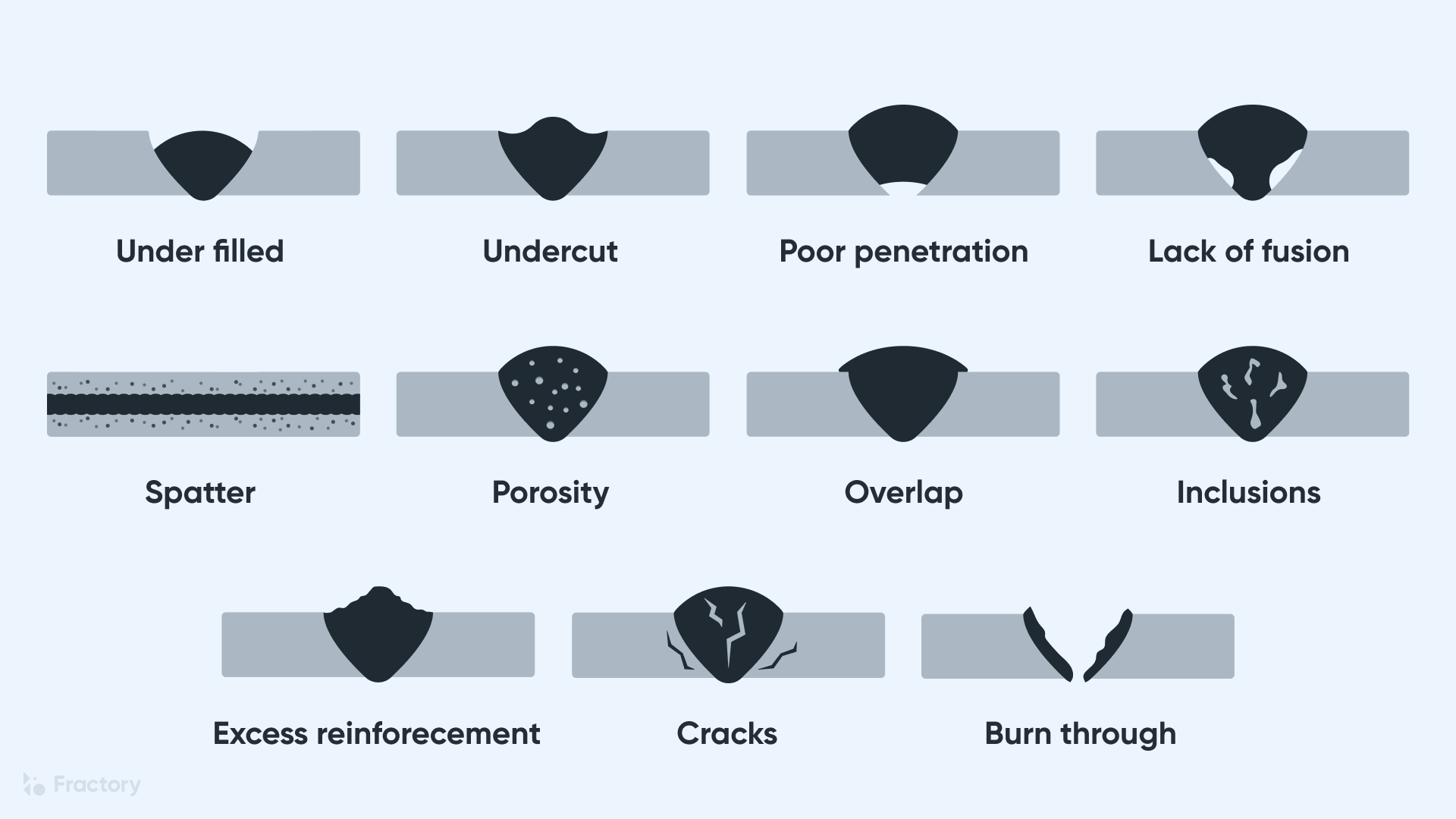
To detect and evaluate porosity, non-destructive screening techniques such as ultrasonic testing or X-ray inspection are often used. These techniques enable the recognition of interior issues without endangering the stability of the weld. By assessing the size, shape, and circulation of porosity within a weld, welders can make educated decisions to enhance their welding procedures and achieve sounder weld joints.
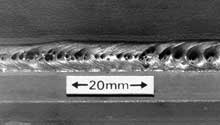
Elements Affecting Porosity Development
The incident of porosity in welding is influenced by a myriad of factors, varying from gas protecting efficiency to the details of welding specification settings. Welding criteria, including voltage, present, travel rate, and weblink electrode kind, also effect porosity formation. The welding strategy used, such as gas metal arc welding (GMAW) or shielded steel arc welding (SMAW), can affect porosity formation due to variants in heat circulation and gas coverage - What is Porosity.
Results of Porosity on Weld Quality
The presence of porosity likewise compromises the weld's resistance to corrosion, as the caught air or gases within the gaps can react with the surrounding atmosphere, leading to deterioration over time. In addition, porosity can hinder the weld's ability to hold up against stress or impact, additional endangering the total quality and dependability of the bonded structure. In essential applications such as aerospace, auto, or structural constructions, where safety and sturdiness are critical, the destructive impacts of porosity on weld top quality can have severe consequences, emphasizing the relevance of minimizing porosity with proper welding techniques and procedures.
Techniques to Minimize Porosity
In addition, utilizing the appropriate welding specifications, such as the correct voltage, present, and travel speed, is vital in protecting against porosity. Maintaining a constant arc size and angle during welding likewise helps lower the chance of porosity.

In addition, picking the best securing gas and preserving appropriate gas flow prices are essential in decreasing porosity. Making use of the proper welding strategy, such as back-stepping or using a weaving activity, can also help distribute warmth uniformly and reduce the possibilities of porosity formation. Lastly, guaranteeing correct air flow in the welding setting to remove any kind of possible resources of contamination is vital for achieving porosity-free welds. By carrying out these methods, welders can successfully reduce porosity and create premium bonded joints.
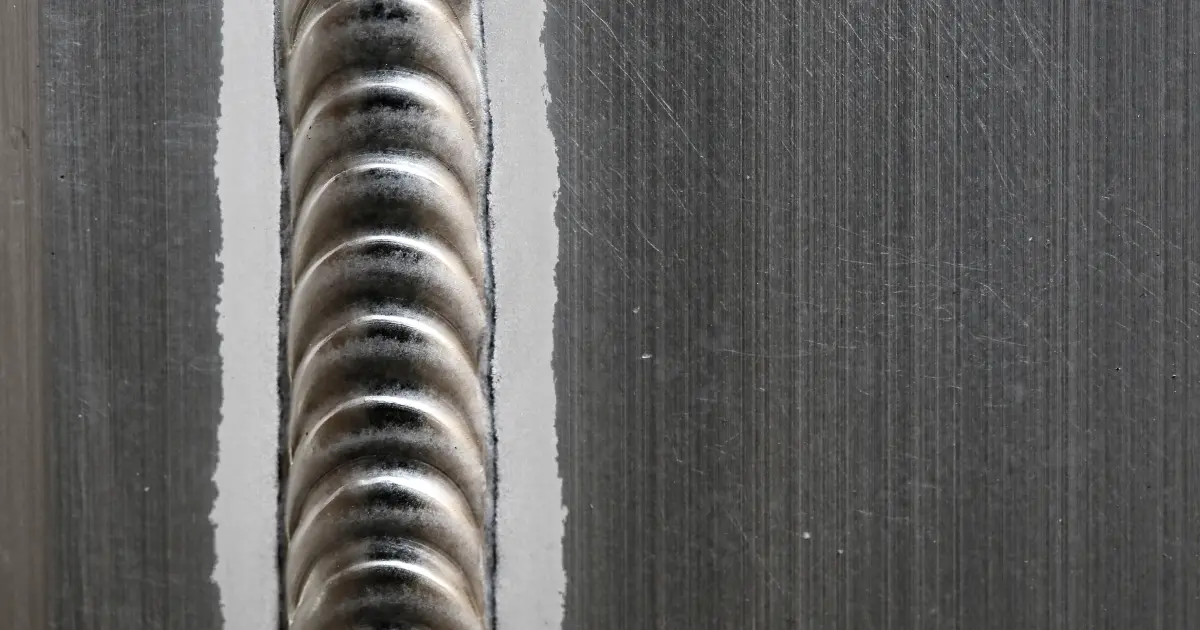
Advanced Solutions for Porosity Control
Executing sophisticated modern technologies and innovative techniques plays a critical role in attaining exceptional control over porosity in welding processes. In addition, using advanced welding techniques such as pulsed MIG welding or changed environment welding can also assist alleviate porosity issues.
An additional advanced service entails using his response innovative welding tools. As an example, making use of devices with integrated functions like waveform control and sophisticated source of power can improve weld high quality and lower porosity dangers. The implementation of automated welding systems with precise control over specifications can considerably decrease porosity issues.
Moreover, integrating advanced tracking and evaluation modern technologies such as real-time X-ray imaging or automated ultrasonic screening can help in finding porosity early in the welding Bonuses process, enabling instant restorative activities. In general, integrating these sophisticated services can greatly enhance porosity control and improve the general top quality of welded parts.
Verdict
In conclusion, understanding the science behind porosity in welding is essential for welders and makers to create high-quality welds - What is Porosity. Advanced remedies for porosity control can even more enhance the welding process and make sure a solid and trustworthy weld.
Report this page